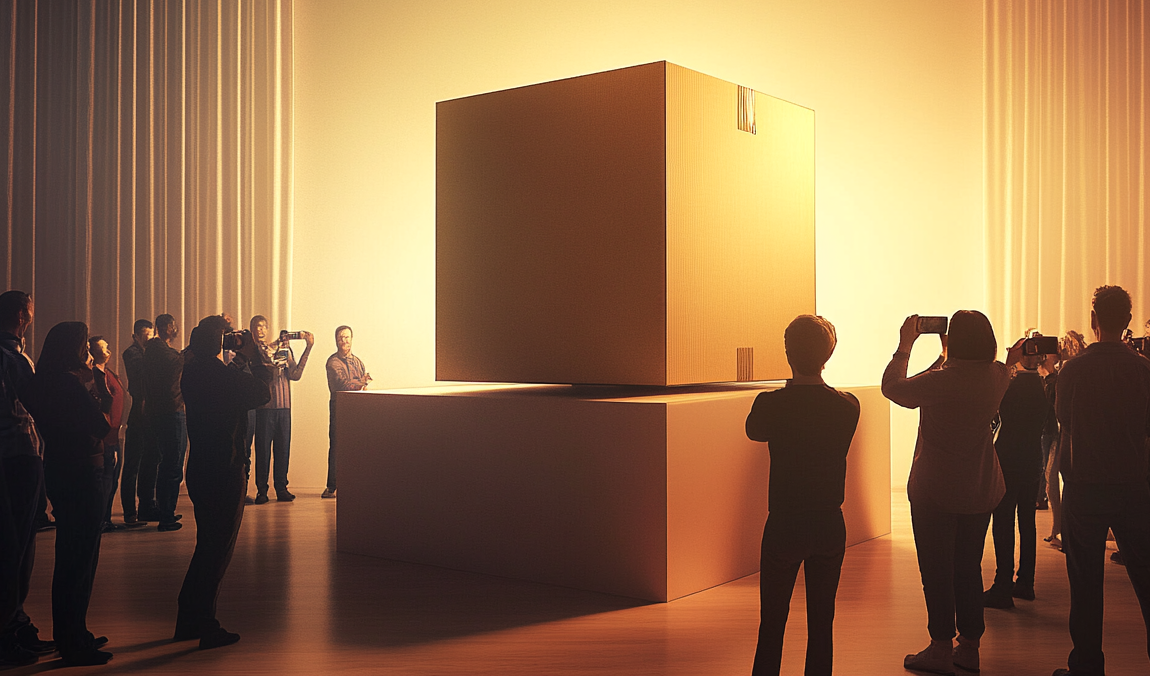
Corrugated boxes are far more than simple containers. For OEMs (Original Equipment Manufacturers) and industrial suppliers, they are essential components of a highly technical logistics ecosystem. The right corrugated packaging can reduce freight damage, lower shipping costs, streamline storage, and improve customer satisfaction. At OEM Materials & Supplies, a leading supplier of stock and custom corrugated packaging in Southern California, we understand that packaging is not a one-size-fits-all solution. This guide explores corrugated packaging in depth—from materials and construction to performance specifications and customization options.
What Are Corrugated Boxes? A Structural Overview
Corrugated boxes are constructed using corrugated fiberboard—a material composed of a fluted corrugated sheet sandwiched between one or two flat linerboards. This design provides strength, cushioning, and flexibility, making it ideal for heavy, sensitive, or irregularly shaped industrial products.
Components of Corrugated Fiberboard
- Linerboard: The flat, outer facings. Typically made of kraft paper, linerboard provides rigidity and printing surfaces.
- Corrugating Medium (Fluting): The wavy, inner layer that creates air pockets for shock absorption.
- Adhesive: Often a starch-based glue used to bond the layers.
Types of Corrugated Board Construction
- Single Face: One linerboard with one layer of fluting. Used for wrapping or cushioning.
- Single Wall: One fluted medium between two linerboards. The most common box type.
- Double Wall: Two layers of fluting sandwiched between three linerboards. Offers higher compression resistance.
- Triple Wall: Three fluted layers and four linerboards. Designed for heavy-duty applications like machinery and bulk shipments.
Corrugated Flute Profiles: Choosing the Right Strength and Thickness
Flute size directly affects the performance of corrugated boxes, including stacking strength, cushioning, and print surface quality.
Flute TypeFlutes per FootThicknessApplicationsA Flute~331/4"Maximum cushioningB Flute~471/8"Puncture resistance, better printingC Flute~393/16"Commonly used in shipping cartonsE Flute~901/16"Folding cartons, better for die-cuttingF Flute~1251/32"Retail packaging, small folding boxes
For OEM and industrial users, C and B flutes are most prevalent due to their balance of crush resistance and printability. Double-wall combinations like BC or EB flutes offer multi-layer protection for fragile or oversized components.
Performance Metrics for Corrugated Packaging
Industrial clients often require packaging that meets strict performance criteria. Below are key metrics used to evaluate corrugated packaging:
Edge Crush Test (ECT)
Measures the vertical compression strength of corrugated board. For example:
- 32 ECT is suitable for lightweight contents (<30 lbs)
- 44 ECT and higher for heavier or stacked shipments
Mullen Burst Test
Measures the force required to puncture the box. Common ratings:
- 200# test: General-purpose shipping cartons
- 275# and above: Heavier industrial products
Box Compression Test (BCT)
Assesses the amount of force a box can handle before collapsing. Essential for pallet stacking.
Cobb Water Absorption Test
Determines how much water the board absorbs in a set time. Important for humid or wet environments.
At OEM Materials & Supplies, we offer boxes rated to your exact load, moisture, and handling requirements—especially for parts and components in industries like aerospace, electronics, and heavy machinery.
Corrugated Box Styles and Manufacturing Processes
Choosing the correct box style is critical for shipping efficiency, product protection, and branding. Common box types include:
Regular Slotted Container (RSC)
- Most popular design.
- All flaps have the same length and meet in the center.
Full Overlap (FOL)
- Outer flaps overlap completely.
- Excellent for stacking and heavy contents.
Half Slotted Container (HSC)
- One set of flaps, often used with a separate lid.
Die-Cut Boxes
- Custom-cut shapes for unique items or insert-fit packaging.
Telescoping Boxes
- Two pieces (top and bottom) that slide over each other.
- Good for long or irregular products.
Custom die-cutting, scoring, and slotting machines at OEM allow us to fabricate precision boxes for any SKU or shipping condition.
Custom Corrugated Packaging for OEM and Industrial Applications
Customization is not just about branding—it’s about performance, fit, and supply chain efficiency. OEM Materials & Supplies specializes in tailor-made solutions that integrate with your operations.
Tailored Structural Engineering
Our packaging engineers design boxes to:
- Reduce void fill and wasted space
- Withstand vibrations, stacking, and compression
- Fit into automation systems and robotic pack lines
Material Customization
Depending on your requirements, we offer:
- Virgin kraft vs. recycled content blends
- Moisture barrier coatings
- Anti-static and ESD-safe liners
- Flame-retardant or chemical-resistant options
Custom Printing and Branding
We use flexographic and digital printing to produce:
- Barcodes and compliance labeling
- Instructional graphics or warning symbols
- Full-color branding to reinforce your identity in the supply chain
Sustainability and Corrugated Packaging
Corrugated materials are among the most sustainable packaging options available.
- Recyclable: Nearly 93% of corrugated materials are recovered for recycling in the U.S.
- Renewable Resources: Made primarily from managed forest pulp and recycled fiber.
- Lightweight: Reduces emissions from freight transport.
OEM Materials & Supplies can support your ESG goals with recyclable, biodegradable, or FSC-certified packaging components.
Common Industries Served with Corrugated Packaging
Our custom and stock boxes support customers in the following sectors:
- Automotive & Aerospace: Heavy-duty crates, ESD-safe liners
- Electronics: Precision-fit inner cartons and shock-absorbent packaging
- Medical Equipment: Sterile barrier corrugated systems
- Metal & Industrial Components: Moisture-resistant or reinforced solutions
- Consumer Goods: Branded retail-ready cartons for big-box shipments
Each industry has its own performance and regulatory standards. Our in-house packaging experts ensure your solution meets them all.
How to Order Corrugated Packaging from OEM Materials & Supplies
We simplify the procurement process for OEM and industrial clients through:
Stock Packaging
Thousands of ready-to-ship SKUs available for quick delivery throughout Southern California.
Custom Packaging Design
Our team collaborates with your engineers and logistics team to create packaging that fits your workflow and product tolerances. We offer:
- On-site consultations
- Prototyping and testing
- Just-in-time delivery schedules
Regional Manufacturing and Warehousing
Our Southern California facility allows for:
- Fast turnaround on prototypes
- Reduced freight costs
- Local service with national scalability
Final Thoughts: Why Corrugated Boxes Are a Smart Investment
Corrugated packaging is not merely a shipping expense—it’s a strategic asset. The right box protects your products, optimizes warehouse space, enhances your brand, and contributes to sustainability goals. Whether you need bulk RSC cartons, custom die-cut inserts, or moisture-resistant double-wall boxes, OEM Materials & Supplies delivers high-performance solutions backed by technical expertise and decades of experience.
Let’s Build Your Custom Corrugated Solution
Need help finding the right corrugated box for your next shipment or product line? Contact OEM Materials & Supplies today for a free consultation with our packaging experts. Whether you're shipping across town or around the world, we’ll make sure your product arrives safely, efficiently, and professionally.