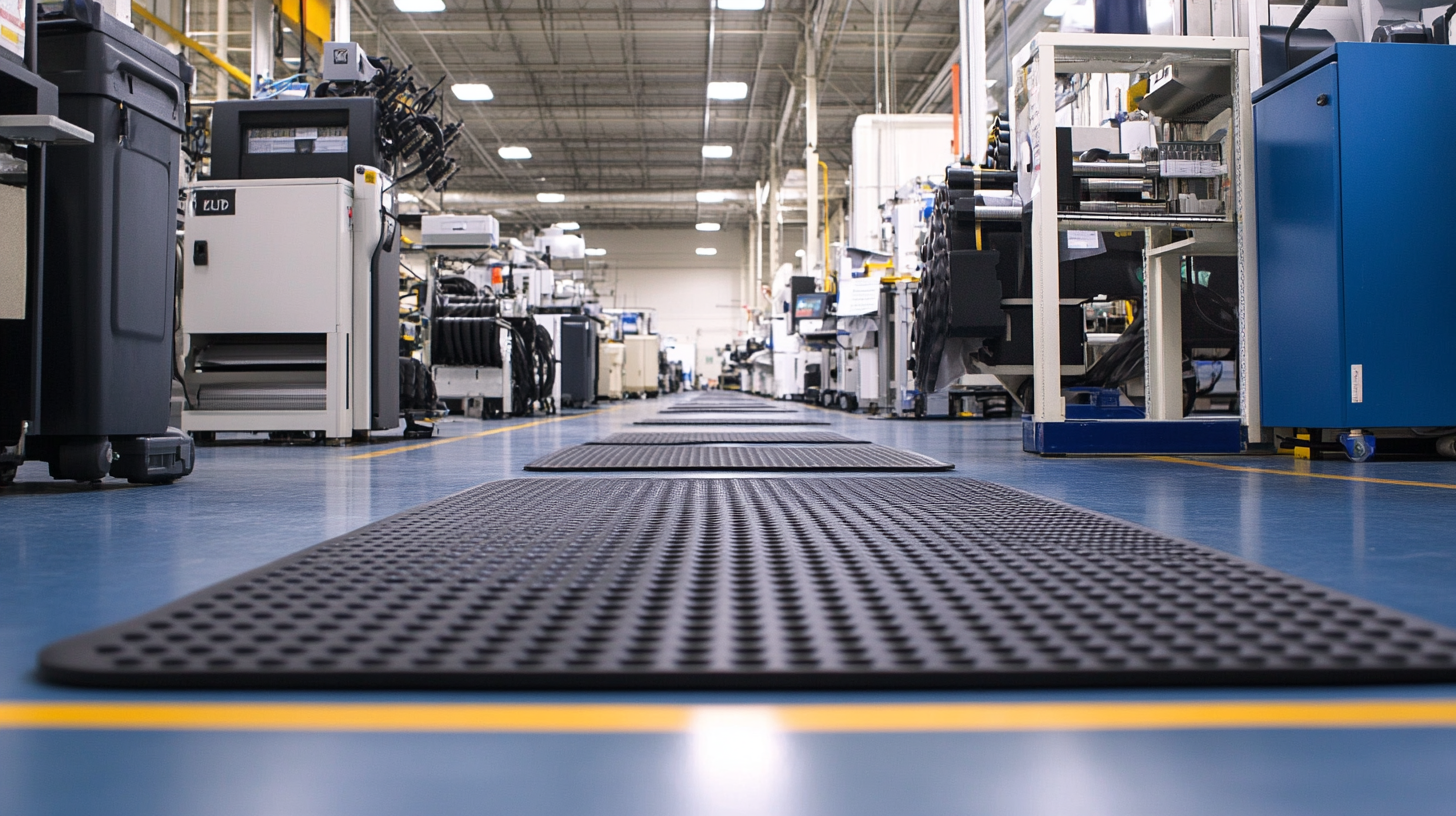
In electronics assembly facilities, even the smallest static discharge can wreak havoc on sensitive components, leading to product failures, increased costs, and customer dissatisfaction. One of the simplest yet most effective tools for mitigating these risks is the use of Electrostatic Discharge (ESD) floor mats. Beyond reducing static events, these mats contribute to higher product quality, improved worker safety, and enhanced morale.
Let’s explore the critical role ESD floor mats play in creating a safer, more efficient, and productive environment for electronics assembly facilities.
1. Understanding ESD and Its Risks
Electrostatic discharge occurs when two objects with different electrical charges come into contact or close proximity, resulting in a sudden transfer of electricity. In electronics assembly, static electricity is a silent threat capable of damaging sensitive components, degrading their performance, or causing complete failure.
The Cost of Static Events
While some static events may result in visible damage, others cause latent defects that compromise product reliability over time. These hidden issues are particularly costly as they lead to warranty claims, product recalls, and damage to brand reputation.
Common Sources of Static
Static electricity can originate from various sources in an assembly environment, including:
- Workers walking across non-ESD-compliant flooring.
- Improper handling of components.
- Friction between materials.
Addressing static at its root is essential to ensuring the integrity of electronics assembly operations.
2. How ESD Floor Mats Reduce Static Events
Static Dissipation
ESD floor mats are specifically designed to dissipate static electricity, preventing it from building up on workers or equipment. These mats are constructed with conductive or dissipative materials that safely redirect static charges away from sensitive areas, neutralizing potential threats.
Creating a Grounded Environment
When used in conjunction with grounding equipment like wrist straps and ESD-safe footwear, ESD mats complete a comprehensive grounding system. This ensures that any residual charge generated by workers is directed away from components and into a grounded source, reducing the likelihood of static-related failures.
Durability and Longevity
High-quality ESD mats are built to withstand heavy foot traffic and repeated use. They maintain their conductivity over time, providing consistent protection against static events even in high-volume production environments.
3. Improving Product Quality with ESD Mats
Reduced Defects
By minimizing the occurrence of static events, ESD mats directly reduce defects and improve the overall quality of assembled products. With fewer damaged components, manufacturers can confidently meet customer expectations and maintain stringent quality standards.
Compliance with Industry Standards
Many industries, including electronics manufacturing, follow strict ESD protection standards such as ANSI/ESD S20.20. ESD floor mats help facilities remain compliant, demonstrating their commitment to quality and reliability.
Supporting Lean Manufacturing
Defect reduction is a cornerstone of lean manufacturing. By preventing static-related failures, ESD mats help facilities eliminate waste, reduce rework, and achieve greater efficiency—all while maintaining high-quality output.
4. Enhancing Worker Safety and Morale
Preventing Static Shocks
While static shocks are typically harmless to people, they can cause discomfort and distraction for workers. ESD mats eliminate these occurrences, creating a more comfortable and focused working environment.
Reducing Fatigue
Many ESD floor mats also feature anti-fatigue properties, providing cushioning and support for workers who stand for long periods. Reduced physical strain leads to higher productivity, lower absenteeism, and improved morale.
Promoting a Culture of Safety
When employees see that their workplace prioritizes safety and provides tools to protect sensitive equipment, it fosters a sense of pride and responsibility. Workers are more likely to follow ESD safety protocols, further reducing risks and contributing to overall operational success.
5. Types of ESD Floor Mats and Their Applications
Table Mats vs. Floor Mats
While ESD table mats protect workstations, ESD floor mats provide a broader scope of protection by addressing static generated through movement across the facility. Used together, these tools create a comprehensive ESD-safe environment.
Portable ESD Mats
For facilities with dynamic layouts, portable ESD mats offer flexibility and convenience. They can be relocated as needed, ensuring that ESD protection adapts to changing workflows.
Customizable Options
ESD mats are available in various sizes, thicknesses, and materials, allowing facilities to choose the best solution for their unique needs. Some mats can even be customized with logos or other features to reinforce safety protocols and branding.
6. Cost-Effectiveness and Long-Term ROI
Reducing Costly Repairs and Rework
Preventing damage to components during assembly eliminates the need for expensive repairs and reduces waste. This directly impacts a facility’s profitability.
Minimizing Downtime
Static-related failures can halt production lines and delay shipments. By mitigating these risks, ESD mats ensure smoother operations and minimize costly downtime.
Extending Equipment Lifespan
ESD protection extends beyond components—it also protects assembly equipment from static-related wear and tear, reducing maintenance costs and prolonging the life of critical machinery.
7. Best Practices for Using ESD Floor Mats
Proper Installation and Grounding
For ESD mats to be effective, they must be properly grounded. Ensure all mats are connected to a reliable grounding point and regularly test their conductivity to maintain performance.
Regular Maintenance
Dust and debris can compromise the conductivity of ESD mats. Regular cleaning with ESD-safe cleaning products ensures mats remain effective over time.
Training Employees
Educate employees on the importance of ESD protection and proper use of ESD mats. Reinforce protocols through regular training and reminders.
A Small Investment with Big Returns
ESD floor mats are a simple yet powerful tool for electronics assembly facilities. By reducing static events, these mats protect sensitive components, improve product quality, and create a safer and more comfortable working environment for employees. With their long-term cost savings and compliance benefits, ESD mats represent a smart investment for any manufacturer looking to optimize operations and enhance profitability.
When it comes to safeguarding your products and your people, ESD floor mats are a solution you can stand on—literally and figuratively.